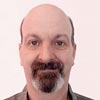
March 29, 2016
In a Quality Management System (QMS) based on ISO 9001, competence and training are an integral part of planning and managing the processes of the QMS. As explained in Using Competence, Training and Awareness to Replace Documentation in your QMS, knowing the competencies required to perform your processes, and closing any gaps between the competency required and the competency of your employees with training, is the backbone of having a well-run process rather than relying on documenting everything. However, in order for this to work properly you need a way to ensure that your training has effectively closed the gaps so that you have the competencies required in your workforce.
In the article Improving quality through effective training, the process of managing your training needs was discussed. This involved identifying the training needs, planning the training, and evaluating the training. Proper management of the training needs is critical if you are to know that the training you have presented is effective.
The very first step needs to be proper identification of the training needs. Without proper identification of the training needs, knowing exactly which competency is needed, how can you verify if the training has been effective? By properly identifying the competencies needed to satisfy the function of your process, your continual improvement needs and the requirements for your quality objectives, you can then compare the competencies you need against the competencies you have in your workforce.
By knowing what competency gap you are trying to resolve, you can more easily compare after your training to see if the competency has been filled. This will tell you if your training was effective.
One simple example of training that is commonly used in ISO 9001 implementation is ISO 9001 awareness training. When you have started to implement ISO 9001, very few people in your organization will understand what a QMS is about, so you will deliver the necessary awareness training to employees. After this training, you will follow up during your process implementation and internal auditing to see that employees now understand better how a QMS works within your organization. It is this follow up that shows you whether the training was effective.
For more information on ISO 9001 awareness training, see ISO 9001 awareness training material: How to create it, what it should contain.
As an example of using training to improve processes in your QMS after implementation, let us say that you have identified that one of your quality objectives is to decrease the cost to perform your processes by making them more efficient and effective. After some investigation, you decide that the best way to do this is to increase the number of small improvements within your processes through the use of the lean manufacturing concept of kaizen: a strategy that incorporates all employees to find incremental changes that will improve the manufacturing process. Since none of your employees understand this lean manufacturing concept, you identify that you have a training need in order to meet this quality objective.
The next logical step is to locate the training you need through an outside training supplier. This training is then delivered to all your employees so that they understand lean manufacturing, and in particular, how kaizen works. This can be done exclusively with the outside training organization, or you could train some internal people who can then train the other staff at your organization. At the end of the training, you can assess if people have learned the skill before they leave the training, which is the first level of verification of effectiveness.
However, after returning from the training you will be having your employees use their new skills. For example, one of the tools is a Kaizen Blitz, where a small group of individuals will work on a process to find ways to improve it in a short amount of time, and you can have several of these sessions throughout your company. These will generate improvements, and subsequent cost savings in your processes.
During this time you will collect data as to the cost savings that have been generated by these process improvements. After a length of time, say several months, this data will show how well your employees have been able to implement their new training towards your objective of decreasing the cost to perform your processes by making them more efficient and effective.
It is only at this point, once you have done this follow up on the effectiveness of your training, that you can know the true effectiveness of your training – when you monitor the process that you wanted to improve by supplying the training to close the competence gap in your organization.
Verifying training effectiveness is something that many companies have troubles with; however, if you are not verifying the effectiveness of training, you are not getting the full benefit from the training. Since training is an investment, you want to know what the return on this investment was so that you can know that your money and time were well spent.
Without following up on your training investment to see if it was effective, you can never be certain that your investment was worth the cost. You owe it to yourself to check your return on investment in training, just like any other investment.
If internal auditor training is one of your competency gaps, why not check out this online ISO 9001:2015 Internal Auditor Course?