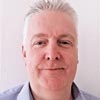
October 26, 2016
Effective communication inside an organization’s OH&SMS can be the difference between success and failure. This became immediately obvious when working with an organization who recently acquired an electrical pallet-lifting truck to cope with a period of rapid business expansion that had to be matched by expansion in their warehouse area, including extra vertical racking space. Immediately on arrival of the new equipment, it was found to be an attraction for staff members, who ranged from curious all the way through to being willing to try and maneuver the new piece of equipment with absolutely no guidance and no training. In summary, this piece of equipment became a hazard, and the area involved became an area of huge risk. So, where does communication come into this real-life situation? Let’s take a look and see:
This allowed the OH&SMS representatives to start a critical process to mitigate the risk presented by the pallet-lifting truck, namely by raising a risk assessment against the situation – with the communication actions listed above recorded as “containment actions,” and followed by arranging training for the drivers, proper signage for the area, and a process document for all employees on how to request materials from the area, stressing that any unauthorized use of this equipment would become a disciplinary offense. Finally, the following communication actions were listed on the conclusion of the corrective action:
All of the above actions were recorded on the OH&SMS and the results set for review at the next group meeting.
As you can see from the example above, effective and timely communication in the OH&SMS is more of a necessity than a benefit. When safeguarding the well-being of employees and the health and safety record of the organization, swift, decisive, and effective communication can be every bit as important as the action to reduce the risk that follows. Like all elements of the OHSAS 18001 standard, effectiveness of communication can and should be reviewed, improvement made, and the fundamentals of the PDCA (Plan, Do, Check, Act) cycle followed. If you underestimate the importance of communication in your OH&SMS, you will ultimately endanger your workforce and stakeholders, and that is something that no organization should be prepared to do.
Why not use our free Gap Analysis Tool to measure your system against the standard?