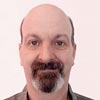
January 27, 2015
Every year we hear about product recalls and consumer alerts about manufactured goods that have major problems, and need to be returned to the company for replacement or refund. In this past year of 2014, there have been recalls of Hewlett-Packard power cords for notebook computers, Graco strollers, and BMW cars for faulty air bags, to name just three. Don’t these companies have a quality management system? Doesn’t a quality management system stop poor-quality products from happening? What is the point of a quality management system if this sort of thing can happen?
The answers to these questions are: Yes, no, and to lower the risk of problems.
Here is an explanation of what I mean:
While not all companies have a quality management system based on ISO 9001, they all have a method of ensuring that they produce and deliver products without defects. Many of the different standards for a quality management system are based on ISO 9001, but all are designed to meet customer requirements and deliver good product. In the case of the three companies mentioned above, all are certified by an approved certification body to have a quality management system compliant with ISO 9001. This means that auditors from an approved outside organization came and verified that the processes of the companies conformed to the requirements of the ISO 9001 standard. If this is the case, then how could these companies have delivered product that was faulty and needed to be recalled from the customer?
Having a quality management system (QMS) that is built around the ISO 9001 requirements provides a framework for a company to identify customer requirements, and then use the principles of the process approach and evidence-based decision making to deliver on these requirements and improve. This means that the company has ensured that customer requirements are identified and that the design of the product meets the requirements. The company then controls, monitors, and measures the processes used throughout the company to make sure they are functioning as planned, and if not, to correct any problems found.
Part of the monitoring and measurement are the products or services of the company. These are under control to identify when non-conforming product occurs, and when it does, to have a documented procedure to control what happens to this non-conforming product and make sure that it is not used without acceptance. Just the existence of a process for dealing with non-conforming material is evidence that a QMS is not expected to completely eliminate the occurrence of product problems, but is there to have a method to control them if they occur.
The QMS is all about identifying the risks in the processes and having methods of controlling these same risks if they should manifest themselves. However, risk reduction is not risk elimination. By having the systems in place to monitor, measure, and control the processes and product, you reduce the risk of a problem occurring by correcting identified problems before they create non-conformances that affect the customer. Having the processes ready to deal with problems in an effective way, and being able to improve due to the identification of problems and potential problems, is how effective businesses use their ISO 9001 quality management systems to gain an advantage and improve profitability.
While a quality management system does not ensure 100% quality product, it does lower the risk of non-conforming product affecting your customers. This is the true advantage of the quality management system, and the reason why you should implement one. By ensuring that you have the appropriate systems in place to monitor for problems, you increase the chances of identifying problems before they affect your customers; it will also mean that when there is a problem, you can retain customer confidence with a systematic method of reacting to correct it. This can help you gain the benefits from your quality management system even when non-conformances occur.
To find out how well your quality management compares to ISO 9001, see ISO 9001 Gap Analysis Tool.