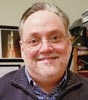
November 14, 2017
Implementation, maintenance, training, and knowledge products for Information Security Management Systems (ISMS) according to the ISO 27001 standard.
Automate your ISMS implementation and maintenance with the Risk Register, Statement of Applicability, and wizards for all required documents.
All required policies, procedures, and forms to implement an ISMS according to ISO 27001.
Train your key people about ISO 27001 requirements and provide cybersecurity awareness training to all of your employees.
Accredited courses for individuals and security professionals who want the highest-quality training and certification.
Get instant answers to any questions related to ISO 27001 and the ISMS using Advisera’s proprietary AI-powered knowledge base.
Compliance and training products for critical infrastructure organizations for the European Union’s Network and Information Systems cybersecurity directive.
All required policies, procedures, and forms to comply with the NIS 2 cybersecurity directive.
Company-wide training program for employees and senior management to comply with Article 20 of the NIS 2 cybersecurity directive.
Compliance and training products for financial entities for the European Union’s DORA regulation.
All required policies, procedures, and forms to comply with the DORA regulation.
Company-wide cybersecurity and resilience training program for all employees, to train them and raise awareness about ICT risk management.
Accredited courses for individuals and DORA professionals who want the highest-quality training and certification.
Compliance and training products for personal data protection according to the European Union’s General Data Protection Regulation.
All required policies, procedures, and forms to comply with the EU GDPR privacy regulation.
Train your key people about GDPR requirements to ensure awareness of data protection principles, privacy rights, and regulatory compliance.
Accredited courses for individuals and privacy professionals who want the highest-quality training and certification.
Implementation, training, and knowledge products for Quality Management Systems (QMS) according to the ISO 9001 standard.
All required policies, procedures, and forms to implement a QMS according to ISO 9001.
Accredited courses for individuals and quality professionals who want the highest-quality training and certification.
Get instant answers to any questions related to ISO 9001 and the QMS using Advisera’s proprietary AI-powered knowledge base.
Implementation, training, and knowledge products for Environmental Management Systems (EMS) according to the ISO 14001 standard.
All required policies, procedures, and forms to implement an EMS according to ISO 14001.
Accredited courses for individuals and environmental professionals who want the highest-quality training and certification.
Get instant answers to any questions related to ISO 14001 and the EMS using Advisera’s proprietary AI-powered knowledge base.
Implementation and training products for Occupational Health & Safety Management Systems (OHSMS) according to the ISO 45001 standard.
All required policies, procedures, and forms to implement an OHSMS according to ISO 45001.
Accredited courses for individuals and health & safety professionals who want the highest-quality training and certification.
Implementation and training products for medical device Quality Management Systems (QMS) according to the ISO 13485 standard.
All required policies, procedures, and forms to implement a medical device QMS according to ISO 13485.
Accredited courses for individuals and medical device professionals who want the highest-quality training and certification.
Compliance products for the European Union’s Medical Device Regulation.
All required policies, procedures, and forms to comply with the EU MDR.
Implementation products for Information Technology Service Management Systems (ITSMS) according to the ISO 20000 standard.
All required policies, procedures, and forms to implement an ITSMS according to ISO 20000.
Implementation products for Business Continuity Management Systems (BCMS) according to the ISO 22301 standard.
All required policies, procedures, and forms to implement a BCMS according to ISO 22301.
Implementation products for testing and calibration laboratories according to the ISO 17025 standard.
All required policies, procedures, and forms to implement ISO 17025 in a laboratory.
Implementation products for automotive Quality Management Systems (QMS) according to the IATF 16949 standard.
All required policies, procedures, and forms to implement an automotive QMS according to IATF 16949.
Implementation products for aerospace Quality Management Systems (QMS) according to the AS9100 standard.
All required policies, procedures, and forms to implement an aerospace QMS according to AS9100.
Implementation, maintenance, training, and knowledge products for consultancies.
Handle multiple ISO 27001 projects by automating repetitive tasks during ISMS implementation.
All required policies, procedures, and forms to implement various standards and regulations for your clients.
Grow your business by organizing cybersecurity and compliance training for your clients under your own brand using Advisera’s learning management system platform.
Accredited Lead Auditor and Lead Implementer courses for ISO standards and DORA, and an advanced course to help consultants grow their business.
Get instant answers to any questions related to ISO 27001 (ISMS), ISO 9001 (QMS), and ISO 14001 (EMS) using Advisera’s proprietary AI-powered knowledge base.
Find new clients, potential partners, and collaborators and meet a community of like-minded professionals locally and globally.
Implementation, maintenance, training, and knowledge products for the IT industry.
Automate your ISMS implementation and maintenance with the Risk Register, Statement of Applicability, and wizards for all required documents.
Documentation to comply with ISO 27001 (cybersecurity), ISO 22301 (business continuity), ISO 20000 (IT service management), GDPR (privacy), NIS 2 (critical infrastructure cybersecurity), and DORA (cybersecurity for financial sector).
Company-wide cybersecurity awareness program for all employees, to decrease incidents and support a successful cybersecurity program.
Accredited courses for individuals and security professionals who want the highest-quality training and certification.
Get instant answers to any questions related to ISO 27001 and the ISMS using Advisera’s proprietary AI-powered knowledge base.
Compliance, training, and knowledge products for essential and important organizations.
Documentation to comply with NIS 2 (cybersecurity), GDPR (privacy), ISO 27001 (cybersecurity), and ISO 22301 (business continuity).
Company-wide cybersecurity awareness program for all employees, to decrease incidents and support a successful cybersecurity program.
Accredited courses for individuals and security professionals who want the highest-quality training and certification.
Get instant answers to any questions related to ISO 27001 and the ISMS using Advisera’s proprietary AI-powered knowledge base.
Implementation, training, and knowledge products for manufacturing companies.
Documentation to comply with ISO 9001 (quality), ISO 14001 (environmental), and ISO 45001 (health & safety), and NIS 2 (critical infrastructure cybersecurity).
Company-wide cybersecurity awareness program for all employees, to decrease incidents and support a successful cybersecurity program.
Accredited courses for individuals and professionals who want the highest-quality training and certification.
Get instant answers to any questions related to ISO 9001 (QMS) and ISO 14001 (EMS) using Advisera’s proprietary AI-powered knowledge base.
Implementation, training, and knowledge products for transportation & distribution companies.
Documentation to comply with ISO 9001 (quality), ISO 14001 (environmental), and ISO 45001 (health & safety), and NIS 2 (critical infrastructure cybersecurity).
Company-wide cybersecurity awareness program for all employees, to decrease incidents and support a successful cybersecurity program.
Accredited courses for individuals and professionals who want the highest-quality training and certification.
Get instant answers to any questions related to ISO 9001 (QMS) and ISO 14001 (EMS) using Advisera’s proprietary AI-powered knowledge base.
Implementation, training, and knowledge products for schools, universities, and other educational organizations.
Documentation to comply with ISO 27001 (cybersecurity), ISO 9001 (quality), and GDPR (privacy).
Company-wide cybersecurity awareness program for all employees, to decrease incidents and support a successful cybersecurity program.
Accredited courses for individuals and professionals who want the highest-quality training and certification.
Get instant answers to any questions related to ISO 27001 (ISMS) and ISO 9001 (QMS) using Advisera’s proprietary AI-powered knowledge base.
Implementation, maintenance, training, and knowledge products for telecoms.
Automate your ISMS implementation and maintenance with the Risk Register, Statement of Applicability, and wizards for all required documents.
Documentation to comply with ISO 27001 (cybersecurity), ISO 22301 (business continuity), ISO 20000 (IT service management), GDPR (privacy), and NIS 2 (critical infrastructure cybersecurity).
Company-wide cybersecurity awareness program for all employees, to decrease incidents and support a successful cybersecurity program.
Accredited courses for individuals and security professionals who want the highest-quality training and certification.
Get instant answers to any questions related to ISO 27001 and the ISMS using Advisera’s proprietary AI-powered knowledge base.
Implementation, maintenance, training, and knowledge products for banks, insurance companies, and other financial organizations.
Automate your ISMS implementation and maintenance with the Risk Register, Statement of Applicability, and wizards for all required documents.
Documentation to comply with DORA (cybersecurity for financial sector), ISO 27001 (cybersecurity), ISO 22301 (business continuity), and GDPR (privacy).
Company-wide cybersecurity awareness program for all employees, to decrease incidents and support a successful cybersecurity program.
Accredited courses for individuals and security professionals who want the highest-quality training and certification.
Get instant answers to any questions related to ISO 27001 and the ISMS using Advisera’s proprietary AI-powered knowledge base.
Implementation, training, and knowledge products for local, regional, and national government entities.
Documentation to comply with ISO 27001 (cybersecurity), ISO 9001 (quality), GDPR (privacy), and NIS 2 (critical infrastructure cybersecurity).
Company-wide cybersecurity awareness program for all employees, to decrease incidents and support a successful cybersecurity program.
Accredited courses for individuals and professionals who want the highest-quality training and certification.
Get instant answers to any questions related to ISO 27001 (ISMS) and ISO 9001 (QMS) using Advisera’s proprietary AI-powered knowledge base.
Implementation, training, and knowledge products for hospitals and other health organizations.
Documentation to comply with ISO 27001 (cybersecurity), ISO 9001 (quality), ISO 14001 (environmental), ISO 45001 (health & safety), NIS 2 (critical infrastructure cybersecurity) and GDPR (privacy).
Company-wide cybersecurity awareness program for all employees, to decrease incidents and support a successful cybersecurity program.
Accredited courses for individuals and professionals who want the highest-quality training and certification.
Get instant answers to any questions related to ISO 27001 (ISMS), ISO 9001 (QMS), and ISO 14001 (EMS) using Advisera’s proprietary AI-powered knowledge base.
Implementation, training, and knowledge products for the medical device industry.
Documentation to comply with MDR and ISO 13485 (medical device), ISO 27001 (cybersecurity), ISO 9001 (quality), ISO 14001 (environmental), ISO 45001 (health & safety), NIS 2 (critical infrastructure cybersecurity) and GDPR (privacy).
Company-wide cybersecurity awareness program for all employees, to decrease incidents and support a successful cybersecurity program.
Accredited courses for individuals and professionals who want the highest-quality training and certification.
Get instant answers to any questions related to ISO 27001 (ISMS), ISO 9001 (QMS), and ISO 14001 (EMS) using Advisera’s proprietary AI-powered knowledge base.
Implementation, training, and knowledge products for the aerospace industry.
Documentation to comply with AS9100 (aerospace), ISO 9001 (quality), ISO 14001 (environmental), and ISO 45001 (health & safety), and NIS 2 (critical infrastructure cybersecurity).
Company-wide cybersecurity awareness program for all employees, to decrease incidents and support a successful cybersecurity program.
Accredited courses for individuals and professionals who want the highest-quality training and certification.
Get instant answers to any questions related to ISO 9001 (QMS) and ISO 14001 (EMS) using Advisera’s proprietary AI-powered knowledge base.
Implementation, training, and knowledge products for the automotive industry.
Documentation to comply with IATF 16949 (automotive), ISO 9001 (quality), ISO 14001 (environmental), and ISO 45001 (health & safety), and NIS 2 (critical infrastructure cybersecurity).
Company-wide cybersecurity awareness program for all employees, to decrease incidents and support a successful cybersecurity program.
Accredited courses for individuals and professionals who want the highest-quality training and certification.
Get instant answers to any questions related to ISO 9001 (QMS) and ISO 14001 (EMS) using Advisera’s proprietary AI-powered knowledge base.
Implementation, training, and knowledge products for laboratories.
Documentation to comply with ISO 17025 (testing and calibration laboratories), ISO 9001 (quality), and NIS 2 (critical infrastructure cybersecurity).
Company-wide cybersecurity awareness program for all employees, to decrease incidents and support a successful cybersecurity program.
Accredited courses for individuals and quality professionals who want the highest-quality training and certification.
Get instant answers to any questions related to ISO 9001 and the QMS using Advisera’s proprietary AI-powered knowledge base.
Effectively using simple risk management tools prevents process defects and achieves continual improvement of the quality management system.
It may be obvious to readers that AS9100 Rev D no longer explicitly requires organizations to have a preventive action system. While this is technically true, risk-based thinking – a preventive concept – is not only required, but expanded to include key product or service realization. Further, AS9100D, paragraph 0.3.1 General, encourages organizations to adopt a process approach when, among other activities, improving the effectiveness of the quality management system.
Through the effective management of process risk, this article explains how to link defect prevention to the requirement of continual improvement. Let’s begin by looking at the constituent parts of all processes.
Quality literature is replete with diagrams illustrating the basic component parts of all processes. No matter which diagram one chooses, they are likely some variation on the following:
Figure 1 – Process Requirements
Successful processes will be supplied on time, from internal and/or external suppliers, with conforming inputs. Each process will supply a conforming output on-time to internal and/or external customers.
After an organization has documented the sequence and interaction of its QMS processes, they can look at the threats to the expected results of output conformity and on-time delivery.
The risk management required in AS9100 Rev D 8.1.1 involves identifying and controlling threats to the successful completion of operational processes. The occurrence of threats is uncertain, and it is the assessment of this uncertainty that is at the heart of risk management. Learn more about risk management in the article 5 key elements of risk management in AS9100 Rev D.
Some useful tools begin by applying the Five Elements of Risk Management shown below. By using a Stop Light Matrix (Figure 2) with a Failure Modes and Effects Analysis (FMEA) organizations will see a clear path to continual improvement.
Element | Description |
1. Identify the risks | Brainstorm the risks to the process output requirements. |
2. Analyze the risks | Use the Stop Light Matrix in Figure 2 to assign the likely impact and probability of each risk. |
3. Evaluate or rank the risks | For each yellow or red risk, use an FMEA to further define the most serious risks. |
4. Mitigate the risk | Implement plans to mitigate the risks above an agreed Risk Priority Number (RPN). |
5. Monitor and review the risk | Did the risk mitigation plans work? If not adjust as needed. |
Table 1 – The Five Elements of Risk Management
Figure 2 – Stop Light Matrix
An FMEA is a well-known tool used by a team of process owners and subject matter experts to assess the likely risk of a design or process failure. In our context, the team reviews each identified risk to the successful completion of the process under consideration. Among others, the risks can be specifically related to one or more inputs to the process being inadequate and/or not on-time. These result in the process itself being subject to unacceptable variation.
For each risk on the FMEA, the team assigns a number from 1-10 that captures:
The resulting three numbers are then multiplied to create an RPN. The higher the resulting RPN, the more significant the risk.
Steps 4 and 5 of the Elements of Risk Management in Table 1 are where the possibility of preventing costly errors moves to the forefront.
Having clearly determined the most serious risks to a process delivering its required outputs on time, the team develops strategies to address any and all variables in the FMEA’s RPN values for each risk. The table below provides some examples of how to decrease severity, likelihood of occurrence and increase the likelihood of detection and preventing possible process failures.
RPN Variable | Actions to address the RPN variable |
Severity of risk (SEV) |
|
Likelihood of occurrence (OCC) |
|
Likelihood of detection (DET) |
|
Table 2 – Reducing FMEA Risk Priority Variables
Optimizing the process by reducing the risks to successful execution should maximize on-time delivery of conforming outputs to internal and external customers. A well-designed and adequately monitored set of process metrics will provide process owners with meaningful indicators of how well a process is operating and how effectively the identified risks are being managed.
Proactively eliminating the risks to the sequence and interaction of the processes will improve the QMS. Work will become less wasteful and more effective.
Beginning with an insightful understanding of the sequence and interaction of its QMS processes, an organization’s process owners and subject matter experts identify the likely risks to the successful completion of those process. With the use of a few simple, proven tools, risks to the successful completion of those processes can be appropriately managed and mitigated. As a result, costly errors will be prevented.
However, it’s important to remember that process risk management is not a “one-and-done” action. As the philosopher Heraclitus observed, “The only thing that is constant is change.” Changes in global markets, the workforce and technology constantly exert pressure on organizations to adapt.
Continual improvement means learning new techniques and updating processes to leverage new information and skills.
To implement AS9100 easily and efficiently, use our AS9100 Premium Documentation toolkit that provides step-by-step guidance and all documents for full AS9100 compliance.
You may unsubscribe at any time. For more information, please see our privacy notice.