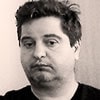
August 27, 2019
Implementation, maintenance, training, and knowledge products for Information Security Management Systems (ISMS) according to the ISO 27001 standard.
Automate your ISMS implementation and maintenance with the Risk Register, Statement of Applicability, and wizards for all required documents.
All required policies, procedures, and forms to implement an ISMS according to ISO 27001.
Train your key people about ISO 27001 requirements and provide cybersecurity awareness training to all of your employees.
Accredited courses for individuals and security professionals who want the highest-quality training and certification.
Get instant answers to any questions related to ISO 27001 and the ISMS using Advisera’s proprietary AI-powered knowledge base.
Compliance and training products for critical infrastructure organizations for the European Union’s Network and Information Systems cybersecurity directive.
All required policies, procedures, and forms to comply with the NIS 2 cybersecurity directive.
Company-wide training program for employees and senior management to comply with Article 20 of the NIS 2 cybersecurity directive.
Compliance and training products for financial entities for the European Union’s DORA regulation.
All required policies, procedures, and forms to comply with the DORA regulation.
Company-wide cybersecurity and resilience training program for all employees, to train them and raise awareness about ICT risk management.
Accredited courses for individuals and DORA professionals who want the highest-quality training and certification.
Compliance and training products for personal data protection according to the European Union’s General Data Protection Regulation.
All required policies, procedures, and forms to comply with the EU GDPR privacy regulation.
Train your key people about GDPR requirements to ensure awareness of data protection principles, privacy rights, and regulatory compliance.
Accredited courses for individuals and privacy professionals who want the highest-quality training and certification.
Implementation, training, and knowledge products for Quality Management Systems (QMS) according to the ISO 9001 standard.
All required policies, procedures, and forms to implement a QMS according to ISO 9001.
Accredited courses for individuals and quality professionals who want the highest-quality training and certification.
Get instant answers to any questions related to ISO 9001 and the QMS using Advisera’s proprietary AI-powered knowledge base.
Implementation, training, and knowledge products for Environmental Management Systems (EMS) according to the ISO 14001 standard.
All required policies, procedures, and forms to implement an EMS according to ISO 14001.
Accredited courses for individuals and environmental professionals who want the highest-quality training and certification.
Get instant answers to any questions related to ISO 14001 and the EMS using Advisera’s proprietary AI-powered knowledge base.
Implementation and training products for Occupational Health & Safety Management Systems (OHSMS) according to the ISO 45001 standard.
All required policies, procedures, and forms to implement an OHSMS according to ISO 45001.
Accredited courses for individuals and health & safety professionals who want the highest-quality training and certification.
Implementation and training products for medical device Quality Management Systems (QMS) according to the ISO 13485 standard.
All required policies, procedures, and forms to implement a medical device QMS according to ISO 13485.
Accredited courses for individuals and medical device professionals who want the highest-quality training and certification.
Compliance products for the European Union’s Medical Device Regulation.
All required policies, procedures, and forms to comply with the EU MDR.
Implementation products for Information Technology Service Management Systems (ITSMS) according to the ISO 20000 standard.
All required policies, procedures, and forms to implement an ITSMS according to ISO 20000.
Implementation products for Business Continuity Management Systems (BCMS) according to the ISO 22301 standard.
All required policies, procedures, and forms to implement a BCMS according to ISO 22301.
Implementation products for testing and calibration laboratories according to the ISO 17025 standard.
All required policies, procedures, and forms to implement ISO 17025 in a laboratory.
Implementation products for automotive Quality Management Systems (QMS) according to the IATF 16949 standard.
All required policies, procedures, and forms to implement an automotive QMS according to IATF 16949.
Implementation products for aerospace Quality Management Systems (QMS) according to the AS9100 standard.
All required policies, procedures, and forms to implement an aerospace QMS according to AS9100.
Implementation, maintenance, training, and knowledge products for consultancies.
Handle multiple ISO 27001 projects by automating repetitive tasks during ISMS implementation.
All required policies, procedures, and forms to implement various standards and regulations for your clients.
Grow your business by organizing cybersecurity and compliance training for your clients under your own brand using Advisera’s learning management system platform.
Accredited DORA, ISO 27001, 9001, 14001, 45001, and 13485 courses for professionals who want the highest-quality training and recognized certification.
Get instant answers to any questions related to ISO 27001 (ISMS), ISO 9001 (QMS), and ISO 14001 (EMS) using Advisera’s proprietary AI-powered knowledge base.
Find new clients, potential partners, and collaborators and meet a community of like-minded professionals locally and globally.
Implementation, maintenance, training, and knowledge products for the IT industry.
Automate your ISMS implementation and maintenance with the Risk Register, Statement of Applicability, and wizards for all required documents.
Documentation to comply with ISO 27001 (cybersecurity), ISO 22301 (business continuity), ISO 20000 (IT service management), GDPR (privacy), NIS 2 (critical infrastructure cybersecurity), and DORA (cybersecurity for financial sector).
Company-wide cybersecurity awareness program for all employees, to decrease incidents and support a successful cybersecurity program.
Accredited courses for individuals and security professionals who want the highest-quality training and certification.
Get instant answers to any questions related to ISO 27001 and the ISMS using Advisera’s proprietary AI-powered knowledge base.
Compliance, training, and knowledge products for essential and important organizations.
Documentation to comply with NIS 2 (cybersecurity), GDPR (privacy), ISO 27001 (cybersecurity), and ISO 22301 (business continuity).
Company-wide cybersecurity awareness program for all employees, to decrease incidents and support a successful cybersecurity program.
Accredited courses for individuals and security professionals who want the highest-quality training and certification.
Get instant answers to any questions related to ISO 27001 and the ISMS using Advisera’s proprietary AI-powered knowledge base.
Implementation, training, and knowledge products for manufacturing companies.
Documentation to comply with ISO 9001 (quality), ISO 14001 (environmental), and ISO 45001 (health & safety), and NIS 2 (critical infrastructure cybersecurity).
Company-wide cybersecurity awareness program for all employees, to decrease incidents and support a successful cybersecurity program.
Accredited courses for individuals and professionals who want the highest-quality training and certification.
Get instant answers to any questions related to ISO 9001 (QMS) and ISO 14001 (EMS) using Advisera’s proprietary AI-powered knowledge base.
Implementation, training, and knowledge products for transportation & distribution companies.
Documentation to comply with ISO 9001 (quality), ISO 14001 (environmental), and ISO 45001 (health & safety), and NIS 2 (critical infrastructure cybersecurity).
Company-wide cybersecurity awareness program for all employees, to decrease incidents and support a successful cybersecurity program.
Accredited courses for individuals and professionals who want the highest-quality training and certification.
Get instant answers to any questions related to ISO 9001 (QMS) and ISO 14001 (EMS) using Advisera’s proprietary AI-powered knowledge base.
Implementation, training, and knowledge products for schools, universities, and other educational organizations.
Documentation to comply with ISO 27001 (cybersecurity), ISO 9001 (quality), and GDPR (privacy).
Company-wide cybersecurity awareness program for all employees, to decrease incidents and support a successful cybersecurity program.
Accredited courses for individuals and professionals who want the highest-quality training and certification.
Get instant answers to any questions related to ISO 27001 (ISMS) and ISO 9001 (QMS) using Advisera’s proprietary AI-powered knowledge base.
Implementation, maintenance, training, and knowledge products for telecoms.
Automate your ISMS implementation and maintenance with the Risk Register, Statement of Applicability, and wizards for all required documents.
Documentation to comply with ISO 27001 (cybersecurity), ISO 22301 (business continuity), ISO 20000 (IT service management), GDPR (privacy), and NIS 2 (critical infrastructure cybersecurity).
Company-wide cybersecurity awareness program for all employees, to decrease incidents and support a successful cybersecurity program.
Accredited courses for individuals and security professionals who want the highest-quality training and certification.
Get instant answers to any questions related to ISO 27001 and the ISMS using Advisera’s proprietary AI-powered knowledge base.
Implementation, maintenance, training, and knowledge products for banks, insurance companies, and other financial organizations.
Automate your ISMS implementation and maintenance with the Risk Register, Statement of Applicability, and wizards for all required documents.
Documentation to comply with DORA (cybersecurity for financial sector), ISO 27001 (cybersecurity), ISO 22301 (business continuity), and GDPR (privacy).
Company-wide cybersecurity awareness program for all employees, to decrease incidents and support a successful cybersecurity program.
Accredited courses for individuals and security professionals who want the highest-quality training and certification.
Get instant answers to any questions related to ISO 27001 and the ISMS using Advisera’s proprietary AI-powered knowledge base.
Implementation, training, and knowledge products for local, regional, and national government entities.
Documentation to comply with ISO 27001 (cybersecurity), ISO 9001 (quality), GDPR (privacy), and NIS 2 (critical infrastructure cybersecurity).
Company-wide cybersecurity awareness program for all employees, to decrease incidents and support a successful cybersecurity program.
Accredited courses for individuals and professionals who want the highest-quality training and certification.
Get instant answers to any questions related to ISO 27001 (ISMS) and ISO 9001 (QMS) using Advisera’s proprietary AI-powered knowledge base.
Implementation, training, and knowledge products for hospitals and other health organizations.
Documentation to comply with ISO 27001 (cybersecurity), ISO 9001 (quality), ISO 14001 (environmental), ISO 45001 (health & safety), NIS 2 (critical infrastructure cybersecurity) and GDPR (privacy).
Company-wide cybersecurity awareness program for all employees, to decrease incidents and support a successful cybersecurity program.
Accredited courses for individuals and professionals who want the highest-quality training and certification.
Get instant answers to any questions related to ISO 27001 (ISMS), ISO 9001 (QMS), and ISO 14001 (EMS) using Advisera’s proprietary AI-powered knowledge base.
Implementation, training, and knowledge products for the medical device industry.
Documentation to comply with MDR and ISO 13485 (medical device), ISO 27001 (cybersecurity), ISO 9001 (quality), ISO 14001 (environmental), ISO 45001 (health & safety), NIS 2 (critical infrastructure cybersecurity) and GDPR (privacy).
Company-wide cybersecurity awareness program for all employees, to decrease incidents and support a successful cybersecurity program.
Accredited courses for individuals and professionals who want the highest-quality training and certification.
Get instant answers to any questions related to ISO 27001 (ISMS), ISO 9001 (QMS), and ISO 14001 (EMS) using Advisera’s proprietary AI-powered knowledge base.
Implementation, training, and knowledge products for the aerospace industry.
Documentation to comply with AS9100 (aerospace), ISO 9001 (quality), ISO 14001 (environmental), and ISO 45001 (health & safety), and NIS 2 (critical infrastructure cybersecurity).
Company-wide cybersecurity awareness program for all employees, to decrease incidents and support a successful cybersecurity program.
Accredited courses for individuals and professionals who want the highest-quality training and certification.
Get instant answers to any questions related to ISO 9001 (QMS) and ISO 14001 (EMS) using Advisera’s proprietary AI-powered knowledge base.
Implementation, training, and knowledge products for the automotive industry.
Documentation to comply with IATF 16949 (automotive), ISO 9001 (quality), ISO 14001 (environmental), and ISO 45001 (health & safety), and NIS 2 (critical infrastructure cybersecurity).
Company-wide cybersecurity awareness program for all employees, to decrease incidents and support a successful cybersecurity program.
Accredited courses for individuals and professionals who want the highest-quality training and certification.
Get instant answers to any questions related to ISO 9001 (QMS) and ISO 14001 (EMS) using Advisera’s proprietary AI-powered knowledge base.
Implementation, training, and knowledge products for laboratories.
Documentation to comply with ISO 17025 (testing and calibration laboratories), ISO 9001 (quality), and NIS 2 (critical infrastructure cybersecurity).
Company-wide cybersecurity awareness program for all employees, to decrease incidents and support a successful cybersecurity program.
Accredited courses for individuals and quality professionals who want the highest-quality training and certification.
Get instant answers to any questions related to ISO 9001 and the QMS using Advisera’s proprietary AI-powered knowledge base.
Since 2016, when the last update of IATF 16949 occurred, the concept of risks and opportunities in this automotive standard has been brought into the forefront of process approach/quality planning and control. The standard requires an organization to identify and control the risks by deploying preventive actions, to take advantage of opportunities that can arise from the organization’s context in a controlled way (by mitigating the associated risks), and to link several risks to contingency plans (in fact, to deploy contingency plans for them). It appears to be clear, but how we can implement this in a practical way?
The hands-on approach based only on standard explanation is not enough, so here is a bit more about how to implement related requirements and how to address IATF 16949 risks and opportunities.
There are multiple requirements related to risks and opportunities, starting from clause 4.4.1, where the organization is required to determine the processes needed to address risks and opportunities that are determined and transferred as a responsibility of top management, as per the 5.1.2 requirement. In requirements starting from 6.1, it is requested to determine the risks and opportunities needed to be taken into account, to plan actions to address those identified risks and opportunities, and to evaluate their effectiveness.
By also taking into consideration the requirements from clause 4.1, where it is required to analyze the internal and external issues concerning the organization, and clause 4.2, where it is required to determine the needs and expectations of interested parties, we will have to take into account the risks related to:
For more about the context of the organization, read the article How to define the context of the organization in IATF 16949:2016.
All the risks mentioned above have to be considered during development and establishment of the contingency plan – see the 6.1.2.3 IATF requirement. The main goal is to ensure the uninterrupted delivery of parts to customers in the case of special situations.
Requirement 6.1.2.1 defines clearly what we have to do to establish a process for handling nonconformities:
The actions (including data regarding the results of implementation) have to be stored as documented information and transferred as lessons learned for similar processes (to prevent the occurrence of a nonconformity in similar processes). Also, requirement 9.1.3.1 demands us to use data to measure trends and establish actions based on such trends (it is about prioritization). Do not forget that the effectiveness of actions taken to address risks and opportunities has to be presented as an input for the management review (see requirement 9.3.2.- e, about the effectiveness of actions taken to address risks and opportunities).
Learn more about management review in the article How to implement management review according to IATF 16949.
Here is a model for how to implement the requirements:
By using this model, you will start to identify the risks. Then you will analyze each identified risk:
When the risk is related to issues defined in the IATF 16949 contingency plan, then you must document contingency plans for that risk. Extend this approach for the risks with high risk levels, and define contingency plans for them, also. Plan preventive actions, follow their implementation, and check their effectiveness based on the PDCA cycle.
In the end, do not forget to update the risk level (keep a history for all risk levels and the reason for their changes). And finally, consider implementing your system in a lean way – keep everything simple and clear, document clearly the rules you want to implement, use digital tools to share data and information for all employees, and follow the principle of “one click of distance between the employee and the information.”
To implement IATF 16949 easily and efficiently, use our IATF 16949 Documentation Toolkit that provides step-by-step guidance and all documents for full IATF 16949 compliance.
You may unsubscribe at any time. For more information, please see our privacy notice.