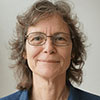
October 12, 2020
If your testing or calibration laboratory is looking to achieve accreditation to ISO/IEC 17025:2017, you may be unclear as to how to practically address the requirement of impartiality and how much effort to go to. This article will assist with this, by providing an overview of what is required by ISO 17025, along with some examples and practical tips.
It is crucial upfront to understand the definition of impartiality. Impartiality is simply defined in ISO/IEC 17025 as the presence of objectivity. This means that the outcome or result of an activity is not compromised by a situation or action of a person.
It is mandatory to identify and address risks to impartiality on an ongoing basis, as part of the general requirements of ISO 17025 implementation. The scope of ISO/IEC 17025:2017 specifically includes impartiality as one of the three elements that the accreditation body will attest to during laboratory accreditation. Along with competence and consistent operation of laboratories, impartiality must be ensured.
The purpose of including the impartiality clause is not only to safeguard the validity of test results or calibration results. The objective is to avoid conflicts of interest and ensure that the management structure, the use of resources, and the execution of processes are implemented and maintained in a way to avoid any compromising situations or actions.
Compromising situations are any situations that could result in a conflict of interest, prejudice, favoritism, one-sidedness, favor, or bias, and that could result in the laboratory not functioning optimally. The impact could be that policies and objectives are made vulnerable, where they would either be damaged (for example, reputation) or weakened (requirements likely to not be met).
Compromising situations could arise from financial, commercial, or other pressures. Threats to impartiality could arise because of:
A practical approach to meeting the ISO 17025:2017 requirements for impartiality is to address it in five main steps. These are a combination of proactive and reactive steps.
A proactive approach is required through structuring and performing laboratory activities in a way to safeguard impartiality, so that personnel are free from both internal and external pressures that may compromise impartiality. A reactive approach may also be required if risks are not foreseen in advance, and a threat is identified later on.
The starting point is awareness and commitment from management:
Follow with personnel awareness:
Step 2. Obtain Personnel Declarations and Commitment
Personnel should sign a code of conduct or some declaration that includes commitment to the impartiality policy. Although prior or current relationships are not necessarily an impartiality risk, possible conflicts of interests should be declared by personnel regarding:
Step 3. Identify and Address Impartiality Risks
Asking personnel to sign a declaration or code of conduct is one action, but not the only action to take. Commitment does not guarantee compliance. Risks to impartiality must be identified on an ongoing basis during routine laboratory activities. This is important as there are ongoing changes to operations, for example taking on new customers, external providers, and personnel, which may result in a new or changed level of risk.
Step 4. Safeguard the Impartiality Status
It is important to manage changes in laboratory activities. Safeguard the impartiality status by considering risks to impartiality upfront during activities such as personnel recruitment, client contracts, and evaluating external providers. For example, during contract review, ask and document the absence or presence of risks, accepted level of risk, and any action taken.
Step 5. Monitor Appropriately
Besides risk assessments, identify and safeguard impartiality on a continual basis in an integrated way, during monitoring and assessment activities. This means that these activities should be integrated into other laboratory activities such as quality meetings, internal audits, root cause analysis, corrective action, and review of the management system.
Following a practical, stepwise approach makes tackling any new activity easier. Your uncertainty of how to address impartiality will be replaced with confidence. Stating your methodical approach upfront, before getting going, provides assurance to all interested parties that you are committed and have a way to address the issue on hand. Review your process more frequently at the beginning, as this will develop your skill and drive improvements.
To comply with all ISO 17025 requirements, use this helpful ISO 17025 Documentation Toolkit that provides all documents for laboratories.