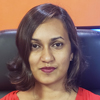
December 5, 2019
Implementation, maintenance, training, and knowledge products for Information Security Management Systems (ISMS) according to the ISO 27001 standard.
Automate your ISMS implementation and maintenance with the Risk Register, Statement of Applicability, and wizards for all required documents.
All required policies, procedures, and forms to implement an ISMS according to ISO 27001.
Train your key people about ISO 27001 requirements and provide cybersecurity awareness training to all of your employees.
Accredited courses for individuals and security professionals who want the highest-quality training and certification.
Get instant answers to any questions related to ISO 27001 and the ISMS using Advisera’s proprietary AI-powered knowledge base.
Compliance and training products for critical infrastructure organizations for the European Union’s Network and Information Systems cybersecurity directive.
All required policies, procedures, and forms to comply with the NIS 2 cybersecurity directive.
Company-wide training program for employees and senior management to comply with Article 20 of the NIS 2 cybersecurity directive.
Compliance and training products for financial entities for the European Union’s DORA regulation.
All required policies, procedures, and forms to comply with the DORA regulation.
Company-wide cybersecurity and resilience training program for all employees, to train them and raise awareness about ICT risk management.
Accredited courses for individuals and DORA professionals who want the highest-quality training and certification.
Compliance and training products for personal data protection according to the European Union’s General Data Protection Regulation.
All required policies, procedures, and forms to comply with the EU GDPR privacy regulation.
Train your key people about GDPR requirements to ensure awareness of data protection principles, privacy rights, and regulatory compliance.
Accredited courses for individuals and privacy professionals who want the highest-quality training and certification.
Implementation, training, and knowledge products for Quality Management Systems (QMS) according to the ISO 9001 standard.
All required policies, procedures, and forms to implement a QMS according to ISO 9001.
Accredited courses for individuals and quality professionals who want the highest-quality training and certification.
Get instant answers to any questions related to ISO 9001 and the QMS using Advisera’s proprietary AI-powered knowledge base.
Implementation, training, and knowledge products for Environmental Management Systems (EMS) according to the ISO 14001 standard.
All required policies, procedures, and forms to implement an EMS according to ISO 14001.
Accredited courses for individuals and environmental professionals who want the highest-quality training and certification.
Get instant answers to any questions related to ISO 14001 and the EMS using Advisera’s proprietary AI-powered knowledge base.
Implementation and training products for Occupational Health & Safety Management Systems (OHSMS) according to the ISO 45001 standard.
All required policies, procedures, and forms to implement an OHSMS according to ISO 45001.
Accredited courses for individuals and health & safety professionals who want the highest-quality training and certification.
Implementation and training products for medical device Quality Management Systems (QMS) according to the ISO 13485 standard.
All required policies, procedures, and forms to implement a medical device QMS according to ISO 13485.
Accredited courses for individuals and medical device professionals who want the highest-quality training and certification.
Compliance products for the European Union’s Medical Device Regulation.
All required policies, procedures, and forms to comply with the EU MDR.
Implementation products for Information Technology Service Management Systems (ITSMS) according to the ISO 20000 standard.
All required policies, procedures, and forms to implement an ITSMS according to ISO 20000.
Implementation products for Business Continuity Management Systems (BCMS) according to the ISO 22301 standard.
All required policies, procedures, and forms to implement a BCMS according to ISO 22301.
Implementation products for testing and calibration laboratories according to the ISO 17025 standard.
All required policies, procedures, and forms to implement ISO 17025 in a laboratory.
Implementation products for automotive Quality Management Systems (QMS) according to the IATF 16949 standard.
All required policies, procedures, and forms to implement an automotive QMS according to IATF 16949.
Implementation products for aerospace Quality Management Systems (QMS) according to the AS9100 standard.
All required policies, procedures, and forms to implement an aerospace QMS according to AS9100.
Implementation, maintenance, training, and knowledge products for consultancies.
Handle multiple ISO 27001 projects by automating repetitive tasks during ISMS implementation.
All required policies, procedures, and forms to implement various standards and regulations for your clients.
Grow your business by organizing cybersecurity and compliance training for your clients under your own brand using Advisera’s learning management system platform.
Accredited Lead Auditor and Lead Implementer courses for ISO standards and DORA, and an advanced course to help consultants grow their business.
Get instant answers to any questions related to ISO 27001 (ISMS), ISO 9001 (QMS), and ISO 14001 (EMS) using Advisera’s proprietary AI-powered knowledge base.
Find new clients, potential partners, and collaborators and meet a community of like-minded professionals locally and globally.
Implementation, maintenance, training, and knowledge products for the IT industry.
Automate your ISMS implementation and maintenance with the Risk Register, Statement of Applicability, and wizards for all required documents.
Documentation to comply with ISO 27001 (cybersecurity), ISO 22301 (business continuity), ISO 20000 (IT service management), GDPR (privacy), NIS 2 (critical infrastructure cybersecurity), and DORA (cybersecurity for financial sector).
Company-wide cybersecurity awareness program for all employees, to decrease incidents and support a successful cybersecurity program.
Accredited courses for individuals and security professionals who want the highest-quality training and certification.
Get instant answers to any questions related to ISO 27001 and the ISMS using Advisera’s proprietary AI-powered knowledge base.
Compliance, training, and knowledge products for essential and important organizations.
Documentation to comply with NIS 2 (cybersecurity), GDPR (privacy), ISO 27001 (cybersecurity), and ISO 22301 (business continuity).
Company-wide cybersecurity awareness program for all employees, to decrease incidents and support a successful cybersecurity program.
Accredited courses for individuals and security professionals who want the highest-quality training and certification.
Get instant answers to any questions related to ISO 27001 and the ISMS using Advisera’s proprietary AI-powered knowledge base.
Implementation, training, and knowledge products for manufacturing companies.
Documentation to comply with ISO 9001 (quality), ISO 14001 (environmental), and ISO 45001 (health & safety), and NIS 2 (critical infrastructure cybersecurity).
Company-wide cybersecurity awareness program for all employees, to decrease incidents and support a successful cybersecurity program.
Accredited courses for individuals and professionals who want the highest-quality training and certification.
Get instant answers to any questions related to ISO 9001 (QMS) and ISO 14001 (EMS) using Advisera’s proprietary AI-powered knowledge base.
Implementation, training, and knowledge products for transportation & distribution companies.
Documentation to comply with ISO 9001 (quality), ISO 14001 (environmental), and ISO 45001 (health & safety), and NIS 2 (critical infrastructure cybersecurity).
Company-wide cybersecurity awareness program for all employees, to decrease incidents and support a successful cybersecurity program.
Accredited courses for individuals and professionals who want the highest-quality training and certification.
Get instant answers to any questions related to ISO 9001 (QMS) and ISO 14001 (EMS) using Advisera’s proprietary AI-powered knowledge base.
Implementation, training, and knowledge products for schools, universities, and other educational organizations.
Documentation to comply with ISO 27001 (cybersecurity), ISO 9001 (quality), and GDPR (privacy).
Company-wide cybersecurity awareness program for all employees, to decrease incidents and support a successful cybersecurity program.
Accredited courses for individuals and professionals who want the highest-quality training and certification.
Get instant answers to any questions related to ISO 27001 (ISMS) and ISO 9001 (QMS) using Advisera’s proprietary AI-powered knowledge base.
Implementation, maintenance, training, and knowledge products for telecoms.
Automate your ISMS implementation and maintenance with the Risk Register, Statement of Applicability, and wizards for all required documents.
Documentation to comply with ISO 27001 (cybersecurity), ISO 22301 (business continuity), ISO 20000 (IT service management), GDPR (privacy), and NIS 2 (critical infrastructure cybersecurity).
Company-wide cybersecurity awareness program for all employees, to decrease incidents and support a successful cybersecurity program.
Accredited courses for individuals and security professionals who want the highest-quality training and certification.
Get instant answers to any questions related to ISO 27001 and the ISMS using Advisera’s proprietary AI-powered knowledge base.
Implementation, maintenance, training, and knowledge products for banks, insurance companies, and other financial organizations.
Automate your ISMS implementation and maintenance with the Risk Register, Statement of Applicability, and wizards for all required documents.
Documentation to comply with DORA (cybersecurity for financial sector), ISO 27001 (cybersecurity), ISO 22301 (business continuity), and GDPR (privacy).
Company-wide cybersecurity awareness program for all employees, to decrease incidents and support a successful cybersecurity program.
Accredited courses for individuals and security professionals who want the highest-quality training and certification.
Get instant answers to any questions related to ISO 27001 and the ISMS using Advisera’s proprietary AI-powered knowledge base.
Implementation, training, and knowledge products for local, regional, and national government entities.
Documentation to comply with ISO 27001 (cybersecurity), ISO 9001 (quality), GDPR (privacy), and NIS 2 (critical infrastructure cybersecurity).
Company-wide cybersecurity awareness program for all employees, to decrease incidents and support a successful cybersecurity program.
Accredited courses for individuals and professionals who want the highest-quality training and certification.
Get instant answers to any questions related to ISO 27001 (ISMS) and ISO 9001 (QMS) using Advisera’s proprietary AI-powered knowledge base.
Implementation, training, and knowledge products for hospitals and other health organizations.
Documentation to comply with ISO 27001 (cybersecurity), ISO 9001 (quality), ISO 14001 (environmental), ISO 45001 (health & safety), NIS 2 (critical infrastructure cybersecurity) and GDPR (privacy).
Company-wide cybersecurity awareness program for all employees, to decrease incidents and support a successful cybersecurity program.
Accredited courses for individuals and professionals who want the highest-quality training and certification.
Get instant answers to any questions related to ISO 27001 (ISMS), ISO 9001 (QMS), and ISO 14001 (EMS) using Advisera’s proprietary AI-powered knowledge base.
Implementation, training, and knowledge products for the medical device industry.
Documentation to comply with MDR and ISO 13485 (medical device), ISO 27001 (cybersecurity), ISO 9001 (quality), ISO 14001 (environmental), ISO 45001 (health & safety), NIS 2 (critical infrastructure cybersecurity) and GDPR (privacy).
Company-wide cybersecurity awareness program for all employees, to decrease incidents and support a successful cybersecurity program.
Accredited courses for individuals and professionals who want the highest-quality training and certification.
Get instant answers to any questions related to ISO 27001 (ISMS), ISO 9001 (QMS), and ISO 14001 (EMS) using Advisera’s proprietary AI-powered knowledge base.
Implementation, training, and knowledge products for the aerospace industry.
Documentation to comply with AS9100 (aerospace), ISO 9001 (quality), ISO 14001 (environmental), and ISO 45001 (health & safety), and NIS 2 (critical infrastructure cybersecurity).
Company-wide cybersecurity awareness program for all employees, to decrease incidents and support a successful cybersecurity program.
Accredited courses for individuals and professionals who want the highest-quality training and certification.
Get instant answers to any questions related to ISO 9001 (QMS) and ISO 14001 (EMS) using Advisera’s proprietary AI-powered knowledge base.
Implementation, training, and knowledge products for the automotive industry.
Documentation to comply with IATF 16949 (automotive), ISO 9001 (quality), ISO 14001 (environmental), and ISO 45001 (health & safety), and NIS 2 (critical infrastructure cybersecurity).
Company-wide cybersecurity awareness program for all employees, to decrease incidents and support a successful cybersecurity program.
Accredited courses for individuals and professionals who want the highest-quality training and certification.
Get instant answers to any questions related to ISO 9001 (QMS) and ISO 14001 (EMS) using Advisera’s proprietary AI-powered knowledge base.
Implementation, training, and knowledge products for laboratories.
Documentation to comply with ISO 17025 (testing and calibration laboratories), ISO 9001 (quality), and NIS 2 (critical infrastructure cybersecurity).
Company-wide cybersecurity awareness program for all employees, to decrease incidents and support a successful cybersecurity program.
Accredited courses for individuals and quality professionals who want the highest-quality training and certification.
Get instant answers to any questions related to ISO 9001 and the QMS using Advisera’s proprietary AI-powered knowledge base.
With the introduction of the 2017 revision of ISO/IEC 17025, which seeks greater alignment with ISO 9001, laboratories now need to implement risk-based thinking in relation to their activities. This was addressed in previous versions of the standard using preventive action, but the introduction of risk-based thinking requires the laboratory to take a formal and strategic look at the specific risks and opportunities it faces.
Because it is a new requirement and the standard does not prescribe how it should be done, many laboratories may be unsure about the steps to be taken to identify, assess, and treat risks and opportunities. This article is intended to provide assistance to laboratories regarding ISO 17025 risk management.
Learn more about what’s new in the 2017 revision in the article ISO/IEC 17025:2005 vs. ISO/IEC 17025:2017 revision: What has changed?
Risk can be defined as uncertainty of the laboratory to meet its objectives, such as customer satisfaction. Nevertheless, uncertainty can be negative (risk) or positive (opportunity). Learn about the five steps in the laboratory risk management process below.
The ISO/IEC 17025 risk management process should be considered a team effort, comprising management, quality personnel, and technical staff. In this step, all the potential problems and opportunities that can arise from laboratory activities must be listed. The following methods are useful at this stage and can be used individually or in combination:
Brainstorming. It enables gathering of opinions on all sources of risk (internal and external). Employees of various ranks should participate in brainstorming, as this ensures the most complete and realistic risk assessment. All ideas are welcome, and none are discarded at this stage of the process.
Process approach. It considers both internal and external influences. Sources are considered by reviewing the inputs and outputs of the process/activity, including management, methods, manpower, materials, machinery, and the environment.
Future scenarios/scenario analysis. It involves creation of various scenarios (positive scenarios/best cases and negative scenarios/worst cases), which form the basis for development of a way of acting. The basis for forecasting should be obtained data, such as from audit reports or from customer feedback and complaints. As an example, an opportunity to expand testing may be identified using customer feedback requesting additional tests.
SWOT Analysis (Strengths, Weaknesses, Opportunities, Threats). It looks at external factors such as market forces and position, as well as internal factors such as unique services offered by the laboratory.
Depending on the complexity of your operations, you may want to conduct a qualitative or quantitative assessment of your risks and opportunities. For qualitative assessments, the team would assign a value of low, medium, or high for each risk identified. The level of risk would depend on factors such as the likelihood that the event would occur, and the severity of the consequences of the event (for example, if the laboratory may be affected financially or its reputation may be hurt).
For a quantitative assessment, determine how critical each risk or opportunity is by assigning a value to the probability/likelihood of occurrence, and the severity of the occurrence (i.e., measure of negative or positive impact). There are 3×3 and 5×5 risk matrices that can assist in the calculation and determination of the level of risk. The laboratory would use separate matrices for risk and for opportunity. Laboratories may assign scores between 1 and 3 for each factor, which, when multiplied, would result in risk values between 1 and 9. For a laboratory with more complex operations, scores between 1 and 5 may be assigned to each factor, resulting in risk values between 1 and 25. The resulting risk (or opportunity) value is indicated as low, medium, or high on the matrix.
At this stage, all parties should agree on which ranking of risks is the best, to determine which is to be addressed first, then second, and so on. Rankings may be based not only on the calculated or assigned risk value, but also availability of resources and the costs to address the risk.
The team will have to recommend and decide on the actions to be taken to address the risks and opportunities identified. Actions can range from taking measures to reduce or eliminate the risks, to doing nothing because the chance of the risk happening is so low. Not all risk analysis needs to result in risk-reduction actions. The team may choose to tackle the easier issues first in order to cross them off the list, but issues that may result in critical risk to the laboratory should not be placed on the back burner.
It is advisable to assign person(s) to be responsible for the actions and a timeframe for them to be completed.
Selected actions must then be implemented within the laboratory. Laboratory management will be responsible for ensuring that resources are provided, that the proposed actions are taken, and that they are having the desired effect.
Learn more about ISO 17025 implementation in the blog Checklist of ISO 17025 implementation steps.
The standard does not require the risk management process to be documented. However, to ensure consistent operations, it is recommended for the laboratory to document the process and retain records as evidence that it was implemented. The procedure can be a simple flow chart, while the actual risk assessment can be documented on a form that lists each risk or opportunity, the potential consequences, the level of risk or risk value, and the actions to be taken. The team should sign and date the form. ISO 31000:2018 is a useful resource that provides guidance for management of risk.
For more about ISO 17025 mandatory documents, read the article List of mandatory documents required by ISO 17025:2017.
It is important to note that risk management is an iterative process, and that the list of risks and opportunities must be reviewed periodically as conditions and resources change within the laboratory, or within the industry or country in which it operates. Above all, analysis of risk and opportunity promotes continuous improvement and will benefit the laboratory in terms of quality — and even profit.
To comply with all ISO 17025 requirements, use this helpful ISO 17025 Documentation Toolkit that provides all documents for laboratories.
You may unsubscribe at any time. For more information, please see our privacy notice.