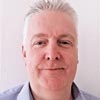
November 11, 2014
Implementation, maintenance, training, and knowledge products for Information Security Management Systems (ISMS) according to the ISO 27001 standard.
Automate your ISMS implementation and maintenance with the Risk Register, Statement of Applicability, and wizards for all required documents.
All required policies, procedures, and forms to implement an ISMS according to ISO 27001.
Train your key people about ISO 27001 requirements and provide cybersecurity awareness training to all of your employees.
Accredited courses for individuals and security professionals who want the highest-quality training and certification.
Get instant answers to any questions related to ISO 27001 and the ISMS using Advisera’s proprietary AI-powered knowledge base.
Compliance and training products for critical infrastructure organizations for the European Union’s Network and Information Systems cybersecurity directive.
All required policies, procedures, and forms to comply with the NIS 2 cybersecurity directive.
Company-wide training program for employees and senior management to comply with Article 20 of the NIS 2 cybersecurity directive.
Compliance and training products for financial entities for the European Union’s DORA regulation.
All required policies, procedures, and forms to comply with the DORA regulation.
Company-wide cybersecurity and resilience training program for all employees, to train them and raise awareness about ICT risk management.
Accredited courses for individuals and DORA professionals who want the highest-quality training and certification.
Compliance and training products for personal data protection according to the European Union’s General Data Protection Regulation.
All required policies, procedures, and forms to comply with the EU GDPR privacy regulation.
Train your key people about GDPR requirements to ensure awareness of data protection principles, privacy rights, and regulatory compliance.
Accredited courses for individuals and privacy professionals who want the highest-quality training and certification.
Implementation, training, and knowledge products for Quality Management Systems (QMS) according to the ISO 9001 standard.
All required policies, procedures, and forms to implement a QMS according to ISO 9001.
Accredited courses for individuals and quality professionals who want the highest-quality training and certification.
Get instant answers to any questions related to ISO 9001 and the QMS using Advisera’s proprietary AI-powered knowledge base.
Implementation, training, and knowledge products for Environmental Management Systems (EMS) according to the ISO 14001 standard.
All required policies, procedures, and forms to implement an EMS according to ISO 14001.
Accredited courses for individuals and environmental professionals who want the highest-quality training and certification.
Get instant answers to any questions related to ISO 14001 and the EMS using Advisera’s proprietary AI-powered knowledge base.
Implementation and training products for Occupational Health & Safety Management Systems (OHSMS) according to the ISO 45001 standard.
All required policies, procedures, and forms to implement an OHSMS according to ISO 45001.
Accredited courses for individuals and health & safety professionals who want the highest-quality training and certification.
Implementation and training products for medical device Quality Management Systems (QMS) according to the ISO 13485 standard.
All required policies, procedures, and forms to implement a medical device QMS according to ISO 13485.
Accredited courses for individuals and medical device professionals who want the highest-quality training and certification.
Compliance products for the European Union’s Medical Device Regulation.
All required policies, procedures, and forms to comply with the EU MDR.
Implementation products for Information Technology Service Management Systems (ITSMS) according to the ISO 20000 standard.
All required policies, procedures, and forms to implement an ITSMS according to ISO 20000.
Implementation products for Business Continuity Management Systems (BCMS) according to the ISO 22301 standard.
All required policies, procedures, and forms to implement a BCMS according to ISO 22301.
Implementation products for testing and calibration laboratories according to the ISO 17025 standard.
All required policies, procedures, and forms to implement ISO 17025 in a laboratory.
Implementation products for automotive Quality Management Systems (QMS) according to the IATF 16949 standard.
All required policies, procedures, and forms to implement an automotive QMS according to IATF 16949.
Implementation products for aerospace Quality Management Systems (QMS) according to the AS9100 standard.
All required policies, procedures, and forms to implement an aerospace QMS according to AS9100.
Implementation, maintenance, training, and knowledge products for consultancies.
Handle multiple ISO 27001 projects by automating repetitive tasks during ISMS implementation.
All required policies, procedures, and forms to implement various standards and regulations for your clients.
Grow your business by organizing cybersecurity and compliance training for your clients under your own brand using Advisera’s learning management system platform.
Accredited Lead Auditor and Lead Implementer courses for ISO standards and DORA, and an advanced course to help consultants grow their business.
Get instant answers to any questions related to ISO 27001 (ISMS), ISO 9001 (QMS), and ISO 14001 (EMS) using Advisera’s proprietary AI-powered knowledge base.
Find new clients, potential partners, and collaborators and meet a community of like-minded professionals locally and globally.
Implementation, maintenance, training, and knowledge products for the IT industry.
Automate your ISMS implementation and maintenance with the Risk Register, Statement of Applicability, and wizards for all required documents.
Documentation to comply with ISO 27001 (cybersecurity), ISO 22301 (business continuity), ISO 20000 (IT service management), GDPR (privacy), NIS 2 (critical infrastructure cybersecurity), and DORA (cybersecurity for financial sector).
Company-wide cybersecurity awareness program for all employees, to decrease incidents and support a successful cybersecurity program.
Accredited courses for individuals and security professionals who want the highest-quality training and certification.
Get instant answers to any questions related to ISO 27001 and the ISMS using Advisera’s proprietary AI-powered knowledge base.
Compliance, training, and knowledge products for essential and important organizations.
Documentation to comply with NIS 2 (cybersecurity), GDPR (privacy), ISO 27001 (cybersecurity), and ISO 22301 (business continuity).
Company-wide cybersecurity awareness program for all employees, to decrease incidents and support a successful cybersecurity program.
Accredited courses for individuals and security professionals who want the highest-quality training and certification.
Get instant answers to any questions related to ISO 27001 and the ISMS using Advisera’s proprietary AI-powered knowledge base.
Implementation, training, and knowledge products for manufacturing companies.
Documentation to comply with ISO 9001 (quality), ISO 14001 (environmental), and ISO 45001 (health & safety), and NIS 2 (critical infrastructure cybersecurity).
Company-wide cybersecurity awareness program for all employees, to decrease incidents and support a successful cybersecurity program.
Accredited courses for individuals and professionals who want the highest-quality training and certification.
Get instant answers to any questions related to ISO 9001 (QMS) and ISO 14001 (EMS) using Advisera’s proprietary AI-powered knowledge base.
Implementation, training, and knowledge products for transportation & distribution companies.
Documentation to comply with ISO 9001 (quality), ISO 14001 (environmental), and ISO 45001 (health & safety), and NIS 2 (critical infrastructure cybersecurity).
Company-wide cybersecurity awareness program for all employees, to decrease incidents and support a successful cybersecurity program.
Accredited courses for individuals and professionals who want the highest-quality training and certification.
Get instant answers to any questions related to ISO 9001 (QMS) and ISO 14001 (EMS) using Advisera’s proprietary AI-powered knowledge base.
Implementation, training, and knowledge products for schools, universities, and other educational organizations.
Documentation to comply with ISO 27001 (cybersecurity), ISO 9001 (quality), and GDPR (privacy).
Company-wide cybersecurity awareness program for all employees, to decrease incidents and support a successful cybersecurity program.
Accredited courses for individuals and professionals who want the highest-quality training and certification.
Get instant answers to any questions related to ISO 27001 (ISMS) and ISO 9001 (QMS) using Advisera’s proprietary AI-powered knowledge base.
Implementation, maintenance, training, and knowledge products for telecoms.
Automate your ISMS implementation and maintenance with the Risk Register, Statement of Applicability, and wizards for all required documents.
Documentation to comply with ISO 27001 (cybersecurity), ISO 22301 (business continuity), ISO 20000 (IT service management), GDPR (privacy), and NIS 2 (critical infrastructure cybersecurity).
Company-wide cybersecurity awareness program for all employees, to decrease incidents and support a successful cybersecurity program.
Accredited courses for individuals and security professionals who want the highest-quality training and certification.
Get instant answers to any questions related to ISO 27001 and the ISMS using Advisera’s proprietary AI-powered knowledge base.
Implementation, maintenance, training, and knowledge products for banks, insurance companies, and other financial organizations.
Automate your ISMS implementation and maintenance with the Risk Register, Statement of Applicability, and wizards for all required documents.
Documentation to comply with DORA (cybersecurity for financial sector), ISO 27001 (cybersecurity), ISO 22301 (business continuity), and GDPR (privacy).
Company-wide cybersecurity awareness program for all employees, to decrease incidents and support a successful cybersecurity program.
Accredited courses for individuals and security professionals who want the highest-quality training and certification.
Get instant answers to any questions related to ISO 27001 and the ISMS using Advisera’s proprietary AI-powered knowledge base.
Implementation, training, and knowledge products for local, regional, and national government entities.
Documentation to comply with ISO 27001 (cybersecurity), ISO 9001 (quality), GDPR (privacy), and NIS 2 (critical infrastructure cybersecurity).
Company-wide cybersecurity awareness program for all employees, to decrease incidents and support a successful cybersecurity program.
Accredited courses for individuals and professionals who want the highest-quality training and certification.
Get instant answers to any questions related to ISO 27001 (ISMS) and ISO 9001 (QMS) using Advisera’s proprietary AI-powered knowledge base.
Implementation, training, and knowledge products for hospitals and other health organizations.
Documentation to comply with ISO 27001 (cybersecurity), ISO 9001 (quality), ISO 14001 (environmental), ISO 45001 (health & safety), NIS 2 (critical infrastructure cybersecurity) and GDPR (privacy).
Company-wide cybersecurity awareness program for all employees, to decrease incidents and support a successful cybersecurity program.
Accredited courses for individuals and professionals who want the highest-quality training and certification.
Get instant answers to any questions related to ISO 27001 (ISMS), ISO 9001 (QMS), and ISO 14001 (EMS) using Advisera’s proprietary AI-powered knowledge base.
Implementation, training, and knowledge products for the medical device industry.
Documentation to comply with MDR and ISO 13485 (medical device), ISO 27001 (cybersecurity), ISO 9001 (quality), ISO 14001 (environmental), ISO 45001 (health & safety), NIS 2 (critical infrastructure cybersecurity) and GDPR (privacy).
Company-wide cybersecurity awareness program for all employees, to decrease incidents and support a successful cybersecurity program.
Accredited courses for individuals and professionals who want the highest-quality training and certification.
Get instant answers to any questions related to ISO 27001 (ISMS), ISO 9001 (QMS), and ISO 14001 (EMS) using Advisera’s proprietary AI-powered knowledge base.
Implementation, training, and knowledge products for the aerospace industry.
Documentation to comply with AS9100 (aerospace), ISO 9001 (quality), ISO 14001 (environmental), and ISO 45001 (health & safety), and NIS 2 (critical infrastructure cybersecurity).
Company-wide cybersecurity awareness program for all employees, to decrease incidents and support a successful cybersecurity program.
Accredited courses for individuals and professionals who want the highest-quality training and certification.
Get instant answers to any questions related to ISO 9001 (QMS) and ISO 14001 (EMS) using Advisera’s proprietary AI-powered knowledge base.
Implementation, training, and knowledge products for the automotive industry.
Documentation to comply with IATF 16949 (automotive), ISO 9001 (quality), ISO 14001 (environmental), and ISO 45001 (health & safety), and NIS 2 (critical infrastructure cybersecurity).
Company-wide cybersecurity awareness program for all employees, to decrease incidents and support a successful cybersecurity program.
Accredited courses for individuals and professionals who want the highest-quality training and certification.
Get instant answers to any questions related to ISO 9001 (QMS) and ISO 14001 (EMS) using Advisera’s proprietary AI-powered knowledge base.
Implementation, training, and knowledge products for laboratories.
Documentation to comply with ISO 17025 (testing and calibration laboratories), ISO 9001 (quality), and NIS 2 (critical infrastructure cybersecurity).
Company-wide cybersecurity awareness program for all employees, to decrease incidents and support a successful cybersecurity program.
Accredited courses for individuals and quality professionals who want the highest-quality training and certification.
Get instant answers to any questions related to ISO 9001 and the QMS using Advisera’s proprietary AI-powered knowledge base.
Most of us, probably at a time in our career where we were less experienced, have needed the help of an ISO 9001 consultant to assist us with the implementation of the standard in the organization where we worked. When you are faced with shaping a quality system and all the accompanying documentation from scratch, it can be extremely daunting, and assistance from anyone with previous experience is always welcome.
However, that implementation stage can be so busy and involved for you that it can pass in a flash, so it’s vitally important that you learn as many lessons as possible with a view to ensuring that you know exactly what to do when that “hired hand” disappears. That consultant also has a part to play, and here is how you can ensure the legacy that remains is a valuable one.
Being involved in your very first ISO 9001 project can be intimidating. As well as the mandatory documents that must be tailored for your organization, and which are dealt with elsewhere in these pages, you also need to educate, implement and ensure that “top management” are committed to the project every step of the way. If work for a large organization or manufacture a complex service or product, you will more than likely develop a tranche of documents with multiple links and references to each other. In all probability you will need corrective action procedures, and internal audits and risk assessments are an integral part of what you will do, at times and frequencies specified by your management and quality teams.
There is so much to remember, and when you do get through your audit, you will feel relieved. But the next morning, that feeling of having to start all over again from scratch can be too familiar. So, how can you avoid this?
I have found that the most efficient method of planning for the future is to establish an “Event Calendar” on day one of your project. Anything that needs to be scheduled can be placed in there, from Quality Meetings, to Risk Assessments and requests and reviews for customer or supplier feedback. When you start to develop your QMS further, you will have management directives to complete more tasks, such as Internal audits, perhaps stretching out as far as the whole year ahead, depending on how your system is structured.
Make sure you capture everything that is required from a policy or anything that “drips down” from the Quality Team meetings or Management Reviews into that calendar. It is likely that the tasks you need to carry out next year will be similar, although the “plan, do, check, act” cycle will ensure that risks and situations change, and your commitment to continual improvement should hopefully mean that next year is not exactly the same as this! You can even schedule when your company cars need serviced, or when the company gas bill is due!
Documenting your routine tasks on the event calendar will accomplish two things for you:
In this way, the day after your audit you can plan your schedule for maintaining compliance for next year. You have a framework of what needs to be achieved and when, and while Quality Meetings and Management Reviews will be used to decide the subject and frequency of some of your tasks, your “Event Calendar” can serve as a “ready reckoner” to tie back the scheduled tasks to your policy, and ensure that you have the correct disciplines going forward.
You can easily click through the pages of your Event Calendar before every Quality meeting for example, to ensure that there is no fundamental practice you have executed last year, but has slipped your mind this year. Perhaps it would even be wise to add this review to your monthly or quarterly meeting? In this way, by the time your audit is over, you already have a firm and documented picture of what needs to be achieved next year to attain the same high standard. Then you really can wave your consultant – and the costs that come with him – goodbye.
To implement ISO 9001 easily and efficiently, use our ISO 9001 Premium Documentation Toolkit that provides step-by-step guidance and all documents for full ISO 9001 compliance.
You may unsubscribe at any time. For more information, please see our privacy notice.