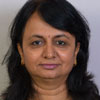
March 8, 2019
Updated: August 28, 2023
Manufacturing medical devices is a highly complex process, and calibration requirements according to ISO 13485, Clause 7.6 (Control of monitoring and measuring equipment), mean high precision and close monitoring. Accuracy of all instruments decays with usage and wear and tear. Factors such as electrical and mechanical shocks or environmental conditions like temperature and humidity may affect the accuracy of measurement. Therefore, a corrective procedure is required to maintain accuracy. In this article, learn more about ISO 13485 calibration requirements and calibration standards.
Calibration of instruments is one of the primary processes used to maintain instrument accuracy. The process of calibration involves configuring an instrument to provide sample measurement results within an acceptable range. This activity requires that a comparison is made between a known reference measurement (the standard equipment), and the measurement using your instrument (test instrument). As a rule of thumb, the accuracy of the calibration standard should be 10 times the accuracy of the measuring device being tested. However, an accuracy ratio of 3:1 is acceptable by most certification bodies.
The instrument used as a reference should be traceable to an instrument that is calibrated to your country’s National Standard; for example, the UK National Standard (UKAS) or the US National Institute of Standards and Technology (NIST). When no such calibration standards exist, the basis used for calibration or verification should be recorded. Calibration is usually followed by an adjustment made to the test instrument so that the output matches that of the standard.
Two important parameters that should be defined for every calibration process are equipment tolerance and the operating range of that instrument. Calibration tolerance is defined as the maximum allowable deviation between a standard of known accuracy and your test instrument. If your equipment exceeds the specified tolerance inaccuracies, it is usually adjusted.
To summarize, calibration quantifies and controls errors and uncertainties within measurement processes and brings them to an acceptable level.
Calibration is required for all instruments, i.e., equipment used in the production of a medical device, that may affect the characteristics of the medical product (dimensions, performance (e.g., volume measurement of spoons for administering antibiotics), or safety (e.g., temperature and humidity in storage)).
Given that manufacturers of medical devices generally do not have the necessary experts or equipment to carry out calibration, this process is usually carried out in accredited laboratories – national metrology institutions or calibration labs. It is the manufacturer’s duty to keep up with the expiration date of the calibration certificate for each piece of equipment, and to initiate the re-calibration process in a timely manner.
Each country or area has its own rules regarding calibration and frequency. In Europe, there is an agency called the European Association of National Metrology Institutes that defines the rules for the way the calibration is carried out and its frequency for each measuring device. Accreditation laboratories in Europe must comply with these guidelines, and it is best to contact them when defining the frequency of re-calibration.
The frequency of calibration is influenced by several factors:
In general, the more often the measuring device is used, the more often it will need to be calibrated. However, frequency also depends on the following factors:
Although the manufacturer of the medical device does not carry out the calibration himself, it is his responsibility to monitor and to be in contact with the laboratory so that they always have a valid measuring instrument.
There are two main ways of performing calibration:
In addition, calibrations can be divided depending on the types of measurements performed by measuring equipment, into:
Most companies have calibration programs that are either in-house or performed externally through a third-party calibration service provider.
Here is a list of practical tips for a calibration program:
When the manufacturer of a medical device receives a calibration certificate from an accreditation laboratory, it is necessary to pay special attention to the part of the certificate that talks about measurement uncertainty. It is a statistical calculation of the possible error that the measuring instrument can make and still be acceptable according to the appropriate calibration standards.
It is the manufacturer’s responsibility to check how high this measurement uncertainty is and whether it affects the measurement area. For example, a medical device must be stored at a temperature of 15°C to 25°C. If a measurement uncertainty of 0.6°C is indicated on the calibration certificate for the thermometer, this means that when the thermometer shows 24.5°C, the temperature in the storage could be as high as 25.1°C, and that is no longer acceptable. Therefore, the manufacturer must incorporate this measurement uncertainty into his procedure for monitoring the temperature in the warehouse.
A well-designed ISO 13485 calibration program as described above helps you maintain the accuracy of your instruments. It also helps you achieve compliance with the ISO 13485 calibration requirements: Clause 7.6 (Control of monitoring and measuring equipment).
To comply with all ISO 13485 requirements, use this helpful ISO 13485 Documentation Toolkit that provides QMS documents for medical device companies.