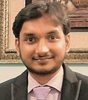
July 4, 2017
Updated: October 24, 2023.
By maintaining the ISO 13485 contamination control procedure and strict control measures, manufacturers can minimize the potential for contamination and uphold the quality and reliability of their medical devices. In this article, find out more about the medical definition of contamination, the cleanliness clause of ISO 13845, and cleanliness standards, procedure, and controls.
The sterilization process should not be confused with the cleaning process. Cleaning is the process of removing dirt, debris, and impurities from surfaces or objects. Sterilization, on the other hand, is the process of killing or eliminating all forms of microorganisms, including bacteria, viruses, and fungi, from surfaces or objects. While cleaning focuses on removing visible contaminants, sterilization aims to achieve a higher level of disinfection by eliminating all potentially harmful microorganisms.
Medical contamination refers to the presence of harmful substances, pathogens, or impurities in medical devices, equipment, or products that can pose risks to patients, healthcare providers, and the overall healthcare system. Manufacturers of medical devices should prioritize contamination control for their devices to ensure the safety and efficacy of their products.
To comply with ISO 13485 requirement 6.4 Contamination control, medical device manufacturers must establish and maintain processes for identifying potential sources of contamination, implementing appropriate controls, and regularly monitoring and verifying the effectiveness of these controls. This includes measures such as proper handling, storage, and sterilization of medical devices, as well as ensuring the cleanliness of manufacturing facilities and equipment.
In the context of quality assurance, contamination can occur at various stages, such as during manufacturing, handling, storage, or transportation. Furthermore, contamination can arise from various sources, including environmental factors, equipment malfunction, human error, or inadequate cleaning and sanitation practices. It can manifest in different forms, such as physical contaminants (e.g., foreign particles, dust), chemical contaminants (e.g., toxins, pollutants), or microbial contaminants (e.g., bacteria, viruses).
A contamination control strategy is a set of measures and protocols implemented to prevent, minimize, or eliminate the introduction and spread of contaminants in a specific environment or process. It involves identifying potential sources of contamination, implementing preventive measures, and establishing procedures for monitoring and controlling contamination levels. A contamination control strategy aims to maintain the cleanliness and integrity of the environment or process to ensure product quality, safety, and reliability. This strategy often includes practices such as regular cleaning and disinfecting, use of protective equipment, proper waste management, and adherence to strict hygiene protocols.
So, what is the most effective way of controlling contaminants? An ISO 13485 contamination control procedure should cover the following aspects:
These measures aim to ensure the production of safe and reliable medical devices and compliance with the ISO 13485 Quality Management System requirements.
Contamination control refers to the measures taken to prevent, reduce, or eliminate the introduction and spread of contaminants in a controlled environment. In the context of ISO 13485 compliance, contamination control is of utmost importance in medical device manufacturing. Contamination in medical devices can lead to various risks, including compromised patient safety, decreased product performance, and regulatory non-compliance. Therefore, implementing robust contamination control measures is crucial to ensure the quality and safety of medical devices.
These measures include procedures such as proper cleaning and sterilization of equipment, maintaining controlled environments, using appropriate personal protective equipment, and implementing strict hygiene practices. They also help prevent the introduction of contaminants, such as microorganisms, particulates, chemicals, or foreign materials, during manufacturing or handling processes.
Benefits of contamination control are:
Overall, contamination control in the medical device industry is vital for ensuring patient safety, maintaining product quality, complying with regulations, building a reputable brand, and achieving cost-effective manufacturing processes.
ISO 13485:2016 focuses on cleanliness during the assembly and packaging processes. Some new requirements have been added in ISO 13485:2016, as compared to the previous standard.
Overall requirements for product cleanliness in ISO 13485:2016 are:
The work environment plays a crucial role in ensuring the quality and safety of the devices produced. A well-designed work environment is essential for efficient production processes, accurate testing, and adherence to strict medical device cleaning regulatory standards. First, a clean and sterile work environment is of the utmost importance in medical device manufacturing. This helps prevent contamination and ensures the integrity of the devices. Strict protocols for cleanliness and hygiene should be followed at all times.
Secondly, the layout and organization of the work area are critical. Proper arrangement of workstations, equipment, and materials can enhance productivity and streamline workflows. Clear labeling of tools and materials also helps reduce impurities and improve efficiency. Furthermore, the availability of proper lighting, ventilation, and temperature control is important to create a comfortable and safe work environment for employees. Adequate lighting ensures accurate visual inspections and reduces the risk of errors. Proper ventilation helps maintain air quality and removes any potentially harmful substances. Controlled temperature levels are crucial for certain manufacturing processes and the storage of sensitive materials.
Examples of work environment practices include the use of cleanrooms, specialized equipment for sterilization, ergonomic workstations, and comprehensive training programs for employees on safety protocols and procedures. Contamination in medical device manufacturing can arise from various sources, such as particles, microorganisms, or chemical residues. These contaminants have the potential to adversely affect the performance, functionality, and biocompatibility of the devices. Moreover, they can pose significant risks to the health and well-being of patients.
To mitigate the risks associated with contamination, stringent control measures must be implemented throughout the manufacturing process. This includes maintaining cleanrooms with controlled air quality, implementing rigorous cleaning and disinfection protocols, and regularly monitoring and validating the effectiveness of these procedures.
Contamination control also extends to the proper handling and storage of raw materials, components, and finished products. Adhering to good manufacturing practices (GMP) and quality management systems (QMS) is essential to minimize the introduction of contaminants and ensure the overall quality and safety of the medical devices.
The whole process of sterilization is in vain if there is contamination during the post-sterilization processes. Therefore, manufacturing and supplying companies must document requirements for control of contamination with microorganisms and particulate substances in the work environment, along with maintaining the mandatory cleanliness throughout the assembly and packaging processes after sterilization. This can be managed with the help of proper ventilation systems, for example, dust collectors, and monitored through air quality tests (based on frequency) on processes after sterilization. Moreover, engineering controls should be in place for containment of sources resulting in contamination.
Requirements of ISO 13485:2016 for work environment and cleanliness in organizations who produce or sell medical devices ensure patients’ safety. Separate lists, with justifications for each category of devices, make the organizational knowledge strong and unambiguous on cleaning requirements for each and every product. Requirements for work environment and contamination controls help the organization to prevent contamination of the product. Therefore, all these requirements basically make the medical device manufacturing, marketing, and supplying processes efficient and safe.
ISO 13485:2016 is making the medical sector safe for all businesses within the supply chain and, ultimately, for the end consumer, i.e., the patient. So, with all these additional requirements, organizations can prove their excellence in the eyes of customers and prove that they really care for patients’ safety.
To implement ISO 13485 easily and efficiently, use our ISO 13485 Documentation Toolkit that provides step-by-step guidance and all documents for full ISO 13485 compliance.
Contributor: Kristina Zvonar Brkic