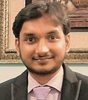
March 21, 2017
Implementation, maintenance, training, and knowledge products for Information Security Management Systems (ISMS) according to the ISO 27001 standard.
Automate your ISMS implementation and maintenance with the Risk Register, Statement of Applicability, and wizards for all required documents.
All required policies, procedures, and forms to implement an ISMS according to ISO 27001.
Train your key people about ISO 27001 requirements and provide cybersecurity awareness training to all of your employees.
Accredited courses for individuals and security professionals who want the highest-quality training and certification.
Get instant answers to any questions related to ISO 27001 and the ISMS using Advisera’s proprietary AI-powered knowledge base.
Compliance and training products for critical infrastructure organizations for the European Union’s Network and Information Systems cybersecurity directive.
All required policies, procedures, and forms to comply with the NIS 2 cybersecurity directive.
Company-wide training program for employees and senior management to comply with Article 20 of the NIS 2 cybersecurity directive.
Compliance and training products for financial entities for the European Union’s DORA regulation.
All required policies, procedures, and forms to comply with the DORA regulation.
Company-wide cybersecurity and resilience training program for all employees, to train them and raise awareness about ICT risk management.
Accredited courses for individuals and DORA professionals who want the highest-quality training and certification.
Compliance and training products for personal data protection according to the European Union’s General Data Protection Regulation.
All required policies, procedures, and forms to comply with the EU GDPR privacy regulation.
Train your key people about GDPR requirements to ensure awareness of data protection principles, privacy rights, and regulatory compliance.
Accredited courses for individuals and privacy professionals who want the highest-quality training and certification.
Implementation, training, and knowledge products for Quality Management Systems (QMS) according to the ISO 9001 standard.
All required policies, procedures, and forms to implement a QMS according to ISO 9001.
Accredited courses for individuals and quality professionals who want the highest-quality training and certification.
Get instant answers to any questions related to ISO 9001 and the QMS using Advisera’s proprietary AI-powered knowledge base.
Implementation, training, and knowledge products for Environmental Management Systems (EMS) according to the ISO 14001 standard.
All required policies, procedures, and forms to implement an EMS according to ISO 14001.
Accredited courses for individuals and environmental professionals who want the highest-quality training and certification.
Get instant answers to any questions related to ISO 14001 and the EMS using Advisera’s proprietary AI-powered knowledge base.
Implementation and training products for Occupational Health & Safety Management Systems (OHSMS) according to the ISO 45001 standard.
All required policies, procedures, and forms to implement an OHSMS according to ISO 45001.
Accredited courses for individuals and health & safety professionals who want the highest-quality training and certification.
Implementation and training products for medical device Quality Management Systems (QMS) according to the ISO 13485 standard.
All required policies, procedures, and forms to implement a medical device QMS according to ISO 13485.
Accredited courses for individuals and medical device professionals who want the highest-quality training and certification.
Compliance products for the European Union’s Medical Device Regulation.
All required policies, procedures, and forms to comply with the EU MDR.
Implementation products for Information Technology Service Management Systems (ITSMS) according to the ISO 20000 standard.
All required policies, procedures, and forms to implement an ITSMS according to ISO 20000.
Implementation products for Business Continuity Management Systems (BCMS) according to the ISO 22301 standard.
All required policies, procedures, and forms to implement a BCMS according to ISO 22301.
Implementation products for testing and calibration laboratories according to the ISO 17025 standard.
All required policies, procedures, and forms to implement ISO 17025 in a laboratory.
Implementation products for automotive Quality Management Systems (QMS) according to the IATF 16949 standard.
All required policies, procedures, and forms to implement an automotive QMS according to IATF 16949.
Implementation products for aerospace Quality Management Systems (QMS) according to the AS9100 standard.
All required policies, procedures, and forms to implement an aerospace QMS according to AS9100.
Implementation, maintenance, training, and knowledge products for consultancies.
Handle multiple ISO 27001 projects by automating repetitive tasks during ISMS implementation.
All required policies, procedures, and forms to implement various standards and regulations for your clients.
Grow your business by organizing cybersecurity and compliance training for your clients under your own brand using Advisera’s learning management system platform.
Accredited DORA, ISO 27001, 9001, 14001, 45001, and 13485 courses for professionals who want the highest-quality training and recognized certification.
Get instant answers to any questions related to ISO 27001 (ISMS), ISO 9001 (QMS), and ISO 14001 (EMS) using Advisera’s proprietary AI-powered knowledge base.
Find new clients, potential partners, and collaborators and meet a community of like-minded professionals locally and globally.
Implementation, maintenance, training, and knowledge products for the IT industry.
Automate your ISMS implementation and maintenance with the Risk Register, Statement of Applicability, and wizards for all required documents.
Documentation to comply with ISO 27001 (cybersecurity), ISO 22301 (business continuity), ISO 20000 (IT service management), GDPR (privacy), NIS 2 (critical infrastructure cybersecurity), and DORA (cybersecurity for financial sector).
Company-wide cybersecurity awareness program for all employees, to decrease incidents and support a successful cybersecurity program.
Accredited courses for individuals and security professionals who want the highest-quality training and certification.
Get instant answers to any questions related to ISO 27001 and the ISMS using Advisera’s proprietary AI-powered knowledge base.
Compliance, training, and knowledge products for essential and important organizations.
Documentation to comply with NIS 2 (cybersecurity), GDPR (privacy), ISO 27001 (cybersecurity), and ISO 22301 (business continuity).
Company-wide cybersecurity awareness program for all employees, to decrease incidents and support a successful cybersecurity program.
Accredited courses for individuals and security professionals who want the highest-quality training and certification.
Get instant answers to any questions related to ISO 27001 and the ISMS using Advisera’s proprietary AI-powered knowledge base.
Implementation, training, and knowledge products for manufacturing companies.
Documentation to comply with ISO 9001 (quality), ISO 14001 (environmental), and ISO 45001 (health & safety), and NIS 2 (critical infrastructure cybersecurity).
Company-wide cybersecurity awareness program for all employees, to decrease incidents and support a successful cybersecurity program.
Accredited courses for individuals and professionals who want the highest-quality training and certification.
Get instant answers to any questions related to ISO 9001 (QMS) and ISO 14001 (EMS) using Advisera’s proprietary AI-powered knowledge base.
Implementation, training, and knowledge products for transportation & distribution companies.
Documentation to comply with ISO 9001 (quality), ISO 14001 (environmental), and ISO 45001 (health & safety), and NIS 2 (critical infrastructure cybersecurity).
Company-wide cybersecurity awareness program for all employees, to decrease incidents and support a successful cybersecurity program.
Accredited courses for individuals and professionals who want the highest-quality training and certification.
Get instant answers to any questions related to ISO 9001 (QMS) and ISO 14001 (EMS) using Advisera’s proprietary AI-powered knowledge base.
Implementation, training, and knowledge products for schools, universities, and other educational organizations.
Documentation to comply with ISO 27001 (cybersecurity), ISO 9001 (quality), and GDPR (privacy).
Company-wide cybersecurity awareness program for all employees, to decrease incidents and support a successful cybersecurity program.
Accredited courses for individuals and professionals who want the highest-quality training and certification.
Get instant answers to any questions related to ISO 27001 (ISMS) and ISO 9001 (QMS) using Advisera’s proprietary AI-powered knowledge base.
Implementation, maintenance, training, and knowledge products for telecoms.
Automate your ISMS implementation and maintenance with the Risk Register, Statement of Applicability, and wizards for all required documents.
Documentation to comply with ISO 27001 (cybersecurity), ISO 22301 (business continuity), ISO 20000 (IT service management), GDPR (privacy), and NIS 2 (critical infrastructure cybersecurity).
Company-wide cybersecurity awareness program for all employees, to decrease incidents and support a successful cybersecurity program.
Accredited courses for individuals and security professionals who want the highest-quality training and certification.
Get instant answers to any questions related to ISO 27001 and the ISMS using Advisera’s proprietary AI-powered knowledge base.
Implementation, maintenance, training, and knowledge products for banks, insurance companies, and other financial organizations.
Automate your ISMS implementation and maintenance with the Risk Register, Statement of Applicability, and wizards for all required documents.
Documentation to comply with DORA (cybersecurity for financial sector), ISO 27001 (cybersecurity), ISO 22301 (business continuity), and GDPR (privacy).
Company-wide cybersecurity awareness program for all employees, to decrease incidents and support a successful cybersecurity program.
Accredited courses for individuals and security professionals who want the highest-quality training and certification.
Get instant answers to any questions related to ISO 27001 and the ISMS using Advisera’s proprietary AI-powered knowledge base.
Implementation, training, and knowledge products for local, regional, and national government entities.
Documentation to comply with ISO 27001 (cybersecurity), ISO 9001 (quality), GDPR (privacy), and NIS 2 (critical infrastructure cybersecurity).
Company-wide cybersecurity awareness program for all employees, to decrease incidents and support a successful cybersecurity program.
Accredited courses for individuals and professionals who want the highest-quality training and certification.
Get instant answers to any questions related to ISO 27001 (ISMS) and ISO 9001 (QMS) using Advisera’s proprietary AI-powered knowledge base.
Implementation, training, and knowledge products for hospitals and other health organizations.
Documentation to comply with ISO 27001 (cybersecurity), ISO 9001 (quality), ISO 14001 (environmental), ISO 45001 (health & safety), NIS 2 (critical infrastructure cybersecurity) and GDPR (privacy).
Company-wide cybersecurity awareness program for all employees, to decrease incidents and support a successful cybersecurity program.
Accredited courses for individuals and professionals who want the highest-quality training and certification.
Get instant answers to any questions related to ISO 27001 (ISMS), ISO 9001 (QMS), and ISO 14001 (EMS) using Advisera’s proprietary AI-powered knowledge base.
Implementation, training, and knowledge products for the medical device industry.
Documentation to comply with MDR and ISO 13485 (medical device), ISO 27001 (cybersecurity), ISO 9001 (quality), ISO 14001 (environmental), ISO 45001 (health & safety), NIS 2 (critical infrastructure cybersecurity) and GDPR (privacy).
Company-wide cybersecurity awareness program for all employees, to decrease incidents and support a successful cybersecurity program.
Accredited courses for individuals and professionals who want the highest-quality training and certification.
Get instant answers to any questions related to ISO 27001 (ISMS), ISO 9001 (QMS), and ISO 14001 (EMS) using Advisera’s proprietary AI-powered knowledge base.
Implementation, training, and knowledge products for the aerospace industry.
Documentation to comply with AS9100 (aerospace), ISO 9001 (quality), ISO 14001 (environmental), and ISO 45001 (health & safety), and NIS 2 (critical infrastructure cybersecurity).
Company-wide cybersecurity awareness program for all employees, to decrease incidents and support a successful cybersecurity program.
Accredited courses for individuals and professionals who want the highest-quality training and certification.
Get instant answers to any questions related to ISO 9001 (QMS) and ISO 14001 (EMS) using Advisera’s proprietary AI-powered knowledge base.
Implementation, training, and knowledge products for the automotive industry.
Documentation to comply with IATF 16949 (automotive), ISO 9001 (quality), ISO 14001 (environmental), and ISO 45001 (health & safety), and NIS 2 (critical infrastructure cybersecurity).
Company-wide cybersecurity awareness program for all employees, to decrease incidents and support a successful cybersecurity program.
Accredited courses for individuals and professionals who want the highest-quality training and certification.
Get instant answers to any questions related to ISO 9001 (QMS) and ISO 14001 (EMS) using Advisera’s proprietary AI-powered knowledge base.
Implementation, training, and knowledge products for laboratories.
Documentation to comply with ISO 17025 (testing and calibration laboratories), ISO 9001 (quality), and NIS 2 (critical infrastructure cybersecurity).
Company-wide cybersecurity awareness program for all employees, to decrease incidents and support a successful cybersecurity program.
Accredited courses for individuals and quality professionals who want the highest-quality training and certification.
Get instant answers to any questions related to ISO 9001 and the QMS using Advisera’s proprietary AI-powered knowledge base.
Medical devices, implants, and surgical instruments are critical healthcare products in which consumers and practitioners look for high precision and accuracy. Therefore, during the production, sales, and other customer-related processes, complaints are a vital and integral part of this industry. Complaint management is an important part of customer relationship management and like every other quality standard, ISO 13485:2016 emphasizes strong controls over complaint handling.
ISO 13485 deals with medical devices, and as the severity of adverse effects of these devices is quite high, the standard emphasizes additional controls for complaint management.
ISO 9001:2015 defines a complaint as an expression of dissatisfaction with a product or service, which is filed by a customer and received by an organization. On the other hand, ISO 13485:2016 specifies the scope of a complaint by defining it as a “written, electronic, or oral communication that alleges deficiencies” in the following aspects of a medical device:
ISO 13485:2016 addresses complaint handling more clearly than ISO 9001:2015 – for example, involving complaints in risk management or identifying complaint-handling procedural requirements. ISO 13485 considers complaints to be one of the mandatory inputs in management review (in the scope of clause 5.6.2 (b)), unlike ISO 9001:2015. Moreover, clause 8.2.2 of ISO 13485:2016 defines the procedural requirements of complaint handling for medical device suppliers.
The organization is mandated, according to ISO 13485:2016, to implement a complaint-handling procedure that addresses the following:
ISO 13485:2016 calls for a vigorous post-market complaint management system, which ensures no complaints are missed. Complaints must be handled in an efficient manner to exceed customer expectations. The new version of ISO 13485:2016 enhances the process approach of the prior version with risk analysis and controlling. For more information on what was changed, see: Infographic: What’s new in the 2016 revision of ISO 13485. Companies lacking a vigorous post-market complaint management system will have to institute processes analogous to those mandated with 21 CFR Section 820 in the U.S. to meet expectations about complaint handling.
Once implemented, ISO 13485 guarantees that no complaints will get lost or customer left to find a solution for himself. The benefits are – your company manages its product and processes, and your customers can depend on a competent partner. Who would wish for more …?
To implement ISO 13485 easily and efficiently, use our ISO 13485 Documentation Toolkit that provides step-by-step guidance and all documents for full ISO 13485 compliance.
You may unsubscribe at any time. For more information, please see our privacy notice.